In Freiburg misst der technologische Vorsprung 14 Meter Länge, 2 Meter Breite, 3 Meter Höhe und ist ein Epitaxieofen. Oft ist davon die Rede, dass Europa technologisch führt, diese Führung aber leider nicht in wettbewerbsfähige Massenproduktion übersetzen würde. Wenn es nach Frank Siebke geht, soll das jetzt anders laufen. Er ist Mitgründer des Unternehmens Nexwafe, in dessen Labor der Koloss steht. Dieser dient der Produktion von Wafern für Siliziumsolarzellen, die ganz anders verläuft als üblich. Wie die Dächer „gotischer Kathedralen“, so beschreibt es Siebke, kommen sie auf dem Band aus der Maschine gefahren, die eine Sonderanfertigung ist und in der 20 Jahre Entwicklungsarbeit stecken.
Frank Siebke, heute Chief Financing Officer von Nexwafe, hat viel vor. Nächstes Jahr soll mit dem Aufbau einer 400 Megawatt Waferfertigung in Bitterfeld begonnen werden, die später auf drei Gigawatt erweitert werden soll. Gleichzeitig sollen mit dem für die Branche revolutionär anmutenden Prozess die Kosten der Wafer auf die Hälfte gesenkt werden, ebenso Siliziumverbrauch und Energiebedarf. „Wir können die CO2-Emissionen selbst mit dem deutschen Energiemix um 80 Prozent reduzieren“, sagt er.
Wie die Photovoltaikproduktion aus Europa verschwunden ist, konnte Frank Siebke über Jahre beobachten. Nachdem er für RWE Schott Solar gearbeitet hatte, wurde er Chief Technology Officer und Investment Direktor bei Good Energies, einem der Hauptinvestoren bei Q-Cells und REC. Aus dem Debakel hat er einiges gelernt und jetzt will er seinen Teil zum Wiederaufbau in Europa beitragen.
Aber ist glaubhaft, was Nexwafe vorhat? Eine Halbierung der Kosten bei gleichzeitiger Produktion in Europa, eine höhere Nachhaltigkeit und wirtschaftlicher Erfolg? Das Geheimnis des Erfolgs soll der revolutionäre Ansatz sein, eine innovative Produktionsmethode, die es bisher noch nicht gibt und für die unsere Jury Nexwafe als „pv magazine highlight top business model“ auszeichnet.
highlights und spotlights
Preis für gute Ideen – das sagt die Jury:
Nexwafe – Revolution soll Kosten von Wafern senken
Es könnte ein Innovationsmärchen aus Deutschland werden. Nach 20 Jahren Forschung, erst an einem Fraunhofer-Institut, dann als Start-up, arbeiten Wissenschaftler daran, drei Prozesse in der Photovoltaik-Wertschöpfungskette zusammenzufassen und nächstes Jahr eine Produktion aufzubauen. Sie scheiden Wafer direkt aus einem Gas ab. Diese sind dünner als herkömmlich und es besteht die Perspektive, dass sie deutlich weniger kosten. Wie das Märchen ausgeht, lässt sich noch nicht sagen. Doch der innovative Ansatz hat die Jury überzeugt, Nexwafe mit dem Prädikat „pv magazine top innovation“ auszuzeichnen.
Die Juroren
Volker Quaschning ist Professor für regenerative Energiesysteme an der HTW Berlin. Hans Urban, Experte für Photovoltaik, Speichertechnik und E-Mobilität, berät Schletter, Maxsolar und Smart Power. Winfried Wahl leitet das Produktmanagement bei Longi Solar in Deutschland.
Mehr Infos, bisherige Preisträger und alles zur Bewerbung unter: www.pv-magazine.de/highlights
Einsendeschluss für die nächste Runde: 8. Oktober 2020
Rund 20 Taximinuten vom Freiburger Hauptbahnhof liegt das TDK-Micronas-Gelände. Frank Siebke hat sich dort eingemietet. An Tor 4 empfängt er seine Gäste. TDK-Micronas hat eine lange Geschichte in der Halbleiterfertigung. „Wir können die Infrastruktur, etwa die Gasversorgung und Lüftungsanlagen nutzen“, sagt Siebke. Beim Gang durch das Gebäude fallen an den Türen Schilder mit weiteren bekannten Namen auf. Auch das Fraunhofer ISE und der Maschinenbauer Rena sind hier mit einigen Laboren präsent.
Wafer ohne Kristallisation und Sägeprozess
Für die Produktion bei Nexwafe zuständig ist Chief Operating Officer Karl Friedrich Haarburger. „Unsere Methode ersetzt etliche Schritte der konventionellen Wafer-Produktion“, sagt er. Bei dieser werden erst Kristalle gezogen und dann zersägt. Bei einem 170 Mikrometer dicken Standard-Wafer fallen 70 Mikrometer Sägespäne an. „Bei Nexwafe können wir die Prozessschritte der Polysilizium-Herstellung, der Kristallisation und des Sägens durch nur einen anderen Schritt ersetzen.“
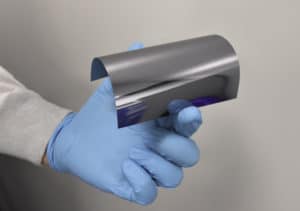
Foto: Nexwafe
Wie das geht, zeigt ein Blick in die Labore einen Stock unter den Büroräumen. Zunächst kauft Nexwafe die monokristallinen Saatwafer. Diese durchlaufen ein Bad, in dem die oberste Schicht des Wafers angeätzt wird. Dann werden sie in die 14 Meter lange Maschine eingeführt, derzeit in der Laborlinie noch per Hand. Sie erhitzt die Wafer. Dadurch entsteht die Struktur, die Siebke als gotische Kathedrale beschreibt: eine hauchdünne monokristalline Siliziumschicht, die auf wenigen nanometergroßen Siliziumsäulen auf dem Saatwafer steht.
Diese so präparierten Saatwafer durchlaufen dann eine 1.200 Grad heiße Kammer, die mit einem Gemisch aus Wasserstoff und Chlorsilan gefüllt ist. In dieser sogenannten Epitaxiekammer scheidet sich dann auf der Oberfläche des Saatwafers kristallines Silizium ab. Je nachdem, wie lange sie in der Beschichtungskammer verweilen, entstehen 50, 100 oder auch 170 Mikrometer dicke monokristalline Wafer. In drei Spuren fahren sie schließlich aus der Linie hinaus. Eine davon ist schon so umgebaut, wie sie in zwei Jahren in der Fabrik realisiert werden soll. Durch Parallelisierung mehrerer Einzelspuren soll eine solche Maschine mit einem Durchsatz von über 5.000 Wafern pro Stunde 80 Mikrometer dünne Wafer herstellen.
Noch sind die neu abgeschiedenen Wafer mit dem Saatwafer verwachsen. Um sie zu trennen, werden in weiteren Maschinen die Kanten besäumt und der gewachsene „EpiWafer“ mechanisch vom Saatwafer getrennt. Die Saatwafer können dann ungefähr 50-mal wiederverwendet werden, bevor sie ersetzt oder wieder aufgearbeitet werden müssen.
Wie so oft in der Photovoltaik, ist der Prozess nicht gänzlich unbekannt. Sony hatte schon 1997 Patente zu dem Prozess eingereicht. Das ISFH und das imec haben auch daran gearbeitet, sagt Siebke. Doch im Gegensatz zu ihnen haben die Institute nur einen sogenannten Batch-Prozess entwickelt, bei dem Wafer in Kammern ein- und wieder ausgefahren werden. Mit Batch-Reaktoren könne man aber nur zwölf Wafer in drei Stunden produzieren. Inline-Prozesse, bei denen Wafer die Maschinen kontinuierlich durchlaufen, haben einen deutlich höheren Durchsatz. „Mit dieser Entwicklung hat das Fraunhofer ISE vor 20 Jahren begonnen“, sagt der CFO. Zusammen mit ihm haben die ISE-Forscher um Stefan Reber 2015 Nexwafe gegründet.
Die Innovation sieht Siebke vor allem in der Entwicklung des kontinuierlichen Inline-Prozesses und darin, diesen schnell gemacht zu haben. Es sind die kleinen technischen Details beim Ätzen, Beschichten und Trennen, über die er deshalb verständlicherweise nicht gerne in der Öffentlichkeit sprechen will.
Er ist gebranntes Kind. Oft hört man den Vorwurf, am Niedergang der Fertigung in Deutschland seien auch die Maschinenbauer Schuld, die das Know-how erst in Zusammenarbeit mit den Solarzellenherstellern erarbeitet und dann mit den Anlagen nach China verkauft hätten. „Wir geben das Know-how nicht mehr aus den Händen“, sagt er daher. Nexwafe werde die Aufträge an Zulieferer so planen und aufteilen, dass keiner den gesamten Prozess kenne und hinterher weiterverkaufen könne. Verkauft würden nur die Wafer – gern in die ganze Welt –, denen man die Geheimnisse der Produktion nicht ansieht.
Expansion nach Bitterfeld
Doch dafür muss das Unternehmen erst einmal wettbewerbsfähig werden. In Bitterfeld hat sich Nexwafe 2018 die ehemaligen Produktionsanlagen der PV Crystalox Solar Silicon GmbH gesichert und für 2019 den Start der Produktion angekündigt. Das hat sich verzögert, gibt Siebke freimütig zu. Zum einen sei es bei einem Teilelieferanten zu Verzögerungen gekommen, dann sei durch den Corona-Lockdown das Labor in Freiburg nicht voll arbeitsfähig gewesen. Daher sei der Umbau der Pilotlinie, mit dem die Hochskalierung erprobt werden soll, erst jetzt abgeschlossen. Nun sei die Kapazität mit einer Million Wafer pro Jahr so hoch, dass genügend Wafer an Zellhersteller zur „Qualifizierung“ geliefert werden könnten. Faktisch wird die Kapazität nicht voll ausgelastet werden, da die Mitarbeiter die Linie vor allem nutzen, um Prozesse zu optimieren.
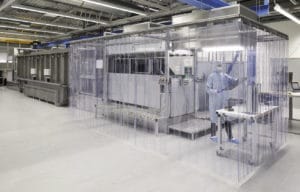
Foto: Nexwafe
Nächstes Jahr solle dann mit dem Bau der neuen Fabrik begonnen werden. Zunächst sollen zwei Abscheideöfen installiert werden, die auf dem Design der Anlage in Freiburg basieren, aber einen deutlich höheren Durchsatz haben. Damit soll es möglich sein, 400 Megawatt im Jahr zu produzieren. Danach sei eine weitere Hochskalierung auf zehn Maschinen und damit auf drei Gigawatt geplant. Die Investitionskosten für beide Schritte veranschlagt er auf 260 Millionen Euro.
Es ist nicht so, dass sich Nexwafe viel Zeit lassen kann. Bereits heute beschäftigt das Unternehmen außer den 25 Mitarbeitern in Freiburg weitere 20 Mitarbeiter in Bitterfeld, die die Gasrecyclinganlagen der früheren Siliziumproduktion in Schuss halten. Daher plant Frank Siebke bald eine weitere Investorenrunde, um die notwendige Finanzierung einzuwerben.
Ob das gelingt, dürfte nicht zuletzt davon abhängen, ob sie sich von der Wettbewerbsfähigkeit überzeugen lassen. Bei großskaliger Produktion im Zig-Gigawatt-Bereich entfallen auf P-Typ-Wafer heute mit rund fünf US-Dollar-Cent pro Watt ein Viertel bis ein Sechstel der Solarmodulkosten. Davon gehen etwas weniger als die Hälfte auf die Kosten für das Polysilizium, etwas mehr als die Hälfte auf die der Herstellung des Einkristalls und das Absägen der Scheiben. Die Wafer werden heute zum größten Teil in Asien produziert. Die Herausforderung, bei diesen Niedrigpreisen mitzuhalten, ist also groß.
Auf der Pro-Seite steht für Nexwafe die Ersparnis beim Silizium. Am Anfang sollen 120 Mikrometer dicke Wafer gefertigt werden. Im Vergleich zu den Standardwafern und den Verlusten beim Sägen würde man also schon die Hälfte des energieaufwendig produzierten Siliziums einsparen. „Schon in dieser Phase werden wir günstiger produzieren“, sagt Siebke. Mit 60 Mikrometer dicken Wafern würde sogar nur noch ein Viertel des Siliziums benötigt.
Auch die Qualität sei besser als bei den konventionellen Verfahren, so Siebke. Das betreffe die Verunreinigung und die Konstanz, die beim spezifischen elektrischen Widerstand und der Dicke erreicht werde. Außerdem können mit dünneren Wafern prinzipiell höhere Wirkungsgrade erreicht werden. Insgesamt seien mehr als zwei Prozent mehr möglich als mit Standard-Wafern, so die Nexwafe-Experten. Außerdem lassen sich P- und N-Typ-Wafer für die gleichen Kosten herstellen. Die Methode reizt ihre Vorteile also am meisten bei dünnen Wafern für N-Typ-Hocheffizienzzellen aus.
Das passt zusammen mit zwei weiteren Projekten in Europa. Ecosolifer hat gerade eine kleine Fertigung von N-Typ-Heterojunction-Zellen im ungarischen Csorna hochgefahren, Meyer Burger will eine solche aufbauen (siehe ab Seiten 29). Bei der Heterojunction-Technologie sieht Siebke die größten Chancen, dass schnell dünnere Wafer eingesetzt werden können. Das liege daran, dass diese auf der Vorder- und Rückseite gleich metallisiert seien. Dadurch komme es zu weniger Verspannungen und die Bruchgefahr sei geringer.
Revolution stößt auf Skepsis
Befragt man andere Experten zu dem Konzept, verweisen diese oft auf das Unternehmen 1366, das ebenfalls dünne Wafer ohne den Umweg über die Kristallisation gewinnt, was schon länger als Zukunftstechnologie bezeichnet wurde, sich aber bisher nicht bewahrheitet hat. Mit ihr können jedoch nur multikristalline Wafer hergestellt werden. Nexwafe produziert dagegen mit einem ganz anderen Verfahren monokristalline Wafer, die für Hocheffizienzzellen notwendig sind, und liegt damit im Gegensatz zu 1366 voll im Markttrend.
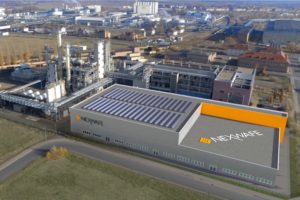
Foto: Nexwafe
Analysten können die Wettbewerbsfähigkeit trotzdem nicht richtig einschätzen, da ihnen die Daten der neuen Prozesse nicht bekannt sind, etwa wie hoch der Durchsatz bei den erwarteten Investitionskosten ist und wie viel Energie wirklich benötigt wird. Außerdem weisen sie darauf hin, dass sich bei der direkten Abscheidung in der Kammer Silizium an den Wänden absetzen und verlorengehen kann. Oder dass die versprochene Homogenität nicht eingehalten werden kann, zu viele Wafer zerbrechen oder Zellhersteller vielleicht gar nicht so dünne Wafer haben wollen. „Der Yield bei der Fertigung dünner Wafer ist einer der Herausforderungen, vor allem, wenn Wafer größer werden, wegen denen Hersteller die Dicke nicht weiter reduziert haben“, sagt Yali Jiang, Analystin bei Bloomberg NEF, „aber die größere Hürde liegt in der Zell- und Modulfertigung“. Viele dieser Schwierigkeiten kann man erst richtig einschätzen, wenn man wirklich in die Massenproduktion einsteigt.
Dazu kommt, dass in der Vergangenheit die Zeit immer gegen neue Technologien gearbeitet hat, indem die konventionellen Methoden immer schneller als gedacht günstiger und besser geworden sind. Das war auch bei der Waferproduktion durch den Recharge-Czochralski-Prozess der Fall, der im großen Maßstab ab 2018 in der Herstellung der Ingots eingesetzt wurde, und durch den Umstieg auf Diamantdrahtsägen im selben Zeitraum, die den Sägeverschnitt deutlich verringerten. Auf dem Markt wird Nexwafe mit Herstellern wie Longi konkurrieren, die eine zigfach größere Produktion haben und seit Jahren die Kosten evolutionär optimieren.
Die Herausforderungen sind also groß. Allerdings sieht es so aus, als ob die großen Hersteller in Asien nicht an ähnlichen Prozessen arbeiten und Nexwafe wirklich ein Alleinstellungsmerkmal hat. Wenn Frank Siebke und seine Kollegen Erfolg haben, könnte die Innovation aus Europa also tatsächlich zu einer Wiedergeburt der Produktion hierzulande führen. „Bei aller Skepsis angesichts der fehlenden Information“, sagt Alex Barrows, „ich kann mir als Marktzugang vorstellen, dass das Endprodukt auf die westlichen Märkte für Hocheffizienzmodule zielt, wo Made in Europe, geringer Materialeinsatz und niedriger CO2-Fußabdruck Kunden motivieren, mehr zu bezahlen.“ Er ist Analyst bei dem Consultingunternehmen Exawatt, das unter anderem zu Wafer-Fertigung berät.
Eine der Fragen ist, ob politische Maßnahmen notwendig sind, die den Produktionsaufbau unterstützen. Zusammen mit Ecosolifer und Sunedison ist Nexwafe beim Konsortium Genuine Green Europe beteiligt, das im Rahmen der Accelerator-Initiative von Solarpower Europe seine Pläne zum Aufbau einer Zwei-Gigawatt-Fertigung vorgestellt hat und zumindest für einen Teil der anvisierten 1 bis 1,2 Milliarden Euro Investitionskosten wohl Unterstützung bei der EU beantragen wird (siehe Seite 30).
Siebke wünscht sich zudem vor allem stabile Rahmenbedingungen für den europäischen Markt. „In der Vergangenheit hatte ich den Eindruck, einige Politiker verhalten sich bei der Energiewende wie Fahranfänger“, sagt er. „Erst geben sie Vollgas, dann würgen sie den Motor ab.“ Er hofft, dass sich das dieses Mal nicht wiederholt und dass zukünftig Umwelt- und Sozialstandards bei der Auswahl von Produkten mehr berücksichtigt werden. So würde ein CO2-Preis oder -Kriterium, wie bei den Ausschreibungen in Frankreich helfen, die Produktion aufzubauen. Notwendig, um nächstes Jahr mit dem Produktionsaufbau zu beginnen, sei das allerdings nicht.
Dieser Inhalt ist urheberrechtlich geschützt und darf nicht kopiert werden. Wenn Sie mit uns kooperieren und Inhalte von uns teilweise nutzen wollen, nehmen Sie bitte Kontakt auf: redaktion@pv-magazine.com.
Diese Nachricht hat mich richtig glücklich gemacht und ich wünsche den Akteuren viel Glück und Erfolg !!! Und sie haben ja die Lektion aus dem Niedergang der europäischen PV-Industrie gelernt – zum Glück ! Aus meiner Sicht fehlt jetzt nur noch das 2. Element: die Wiederaufnahme der Produktion von Bauelementen für Fassaden und Dächer mit integrierter PV, eine Entwicklung in den 90er-Jahren, die leider mit dem EEGvöllig verloren gegangen ist. Da müssen die Bauelemente-Hersteller ran ! Und die Politik muss den Lobbyisten der großen Stromkonzerne trotzen und endlich den Weg frei machen für eine echte Bürger-Energiewende !!!!
Wann ist ein Börsengang geplant?
Würde oben schon gefragt. Aber keine Antwort gegeben.
Ist ein Börsengang geplant, und wann ist damit zu rechnen?
Das funktioniert nur über einen sofortigen Börsengang